Best Way Stone Ltd., Toronto, Canada
Best Way Stone Ltd. is an independent, family-owned business established in 1965, with two modern manufacturing facilities near Toronto, Canada. Best Way Stone supplies high-quality hardscape, and their product range consists of concrete pavers, retaining walls, and masonry products.
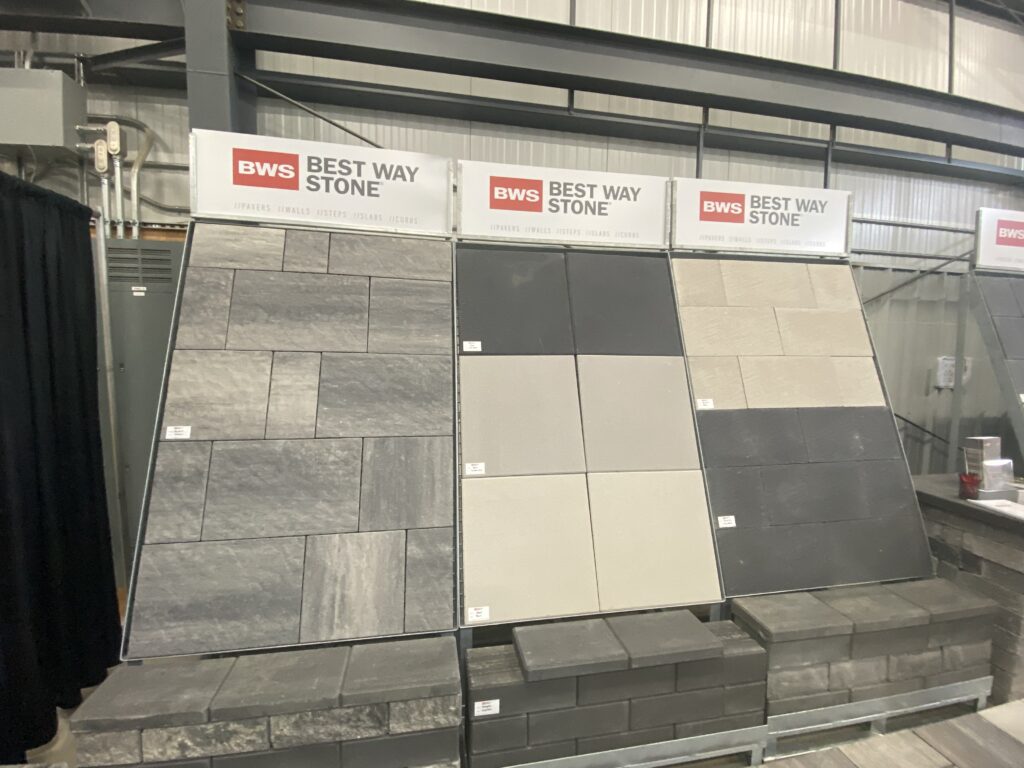
Modern and Energy-efficient Technology for Concrete Production
John Pignatelli, Partner at Best Way Stone was looking for a solution to achieve consistent year-round production in cold canadian climate. As a result of his search for a partner who could deliver that, he contacted Polarmatic Sales Director Kurt Damery to discuss new heating and curing options for their batch plant. Since 2018, Best Way Stone’s Uxbridge plant is equipped with a non-boiler, containerized thermal energy unit TURBOMATIC™.
Polarmatic supplied Best Way Stone with a model PME-MAX 750 G with power of 2.6MBTU (0,75 MW). The TURBOMATIC™ unit melts the ice and snow out of the aggregates in the receiving hopper and heats the aggregates in the bins; 1-2 batches at a time and with no delay in production due to the system’s superior heating power, and without changing the moisture content of the aggregate. The TURBOMATIC™ heats also all hot water needed for the mixing process, and it supplies a preferred warm air curing media with adjustable RH control to their curing kilns – all this with one unit.
According to Mr. Pignatelli, Best Way Stone chose Polarmatic because TURBOMATIC™ system is extremely fuel efficient (60-80% fuel savings). They can now heat both aggregates and water extremely fast, and the system requires little or no operator adjustments. As the all-in-one TURBOMATIC™ aggregate/water heating and curing system basically operates on its own, and as it basically eliminates the need for more people to operate multiple systems, TURBOMATIC™ was a clear choice; “One of the biggest challenges in the concrete industry right now is to staff people”, Mr. Pignatelli adds.
Big Differences in Production
Mr. Pignatelli tells us that they have noticed big differences in their production after starting to use the Polarmatic system; today the warm concrete has a more constant moisture content, and combined with warm air curing, the system contributes to provide consistent colors and no efflorescence in the final products. Compared to results the conventional vapor and steam curing provided them earlier, the difference is big. He also states that they have now experienced higher early strengths in their concrete, and they have been able to double their production during the cold weather months.
In their Woodbridge location, Best Way Stone uses 2 different systems for heating and curing. According to Mr. Pignatelli, the other system is used to heat the aggregate storage piles outside sitting on concrete pads with steam lines fed by a conventional boiler. Heating these piles is very challenging because the loader operator needs to move and turn the material constantly to avoid overheating the aggregates. Another concern with this system is the wasted energy created when the boiler is turned off and the piles are cooling off. The second boiler pumps live wet steam to their curing chambers. Mr. Pignatelli’s biggest concern here is the time loss and condensation; when it is time to unload the cured products, they need to wait to let the moist steam exhaust first, to avoid condensation dripping from the product. In the future, these systems will be replaced by one TURBOMATIC™ unit.
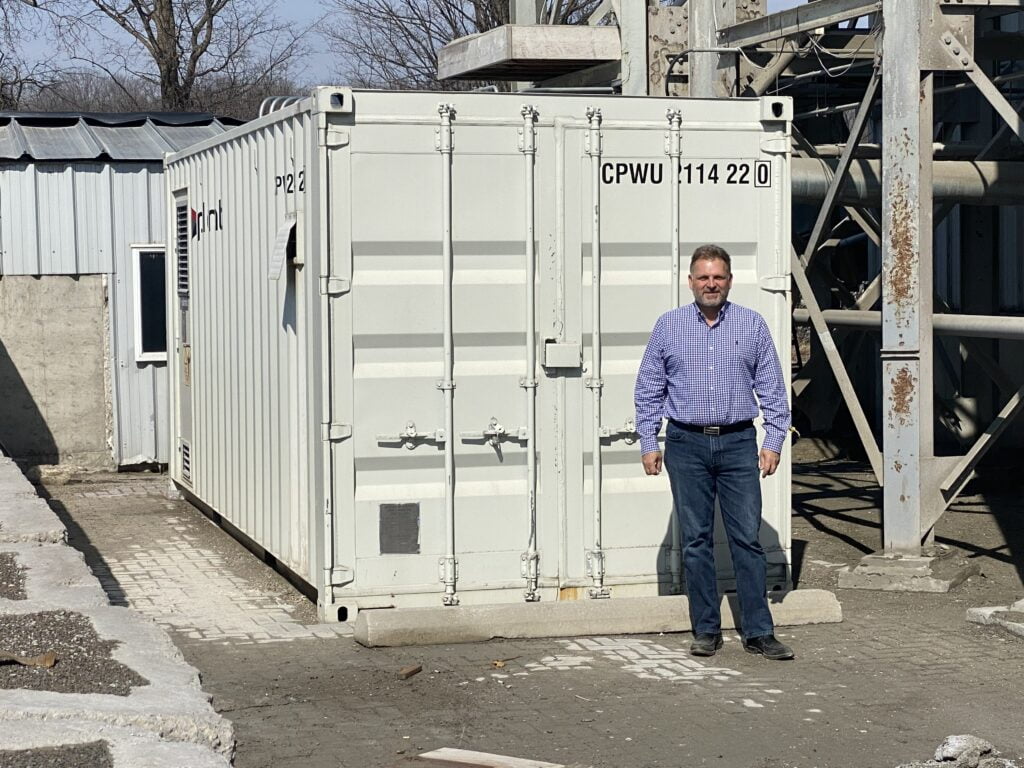
How the TURBOMATIC™ Operates
With the TURBOMATIC™, the frozen aggregates are loaded into the receiving hopper, where they immediately are defrosted after which they will be conveyed ice and snow free to the storage bins inside the plant. Then the sand and stone are heated to the desired temperature and mixed with the heated water the TURBOMATIC™ unit supplies to achieve the desired concrete temperature.
The warm air which is needed for curing the concrete products is produced by the same TURBOMATIC™ unit; the heated hot water recirculates through the heat exchangers inside the air circulation system in the curing chambers. Best Way Stone utilizes an additional water misting system for adjusting the relative humidity of the warm air depending on the cured product.
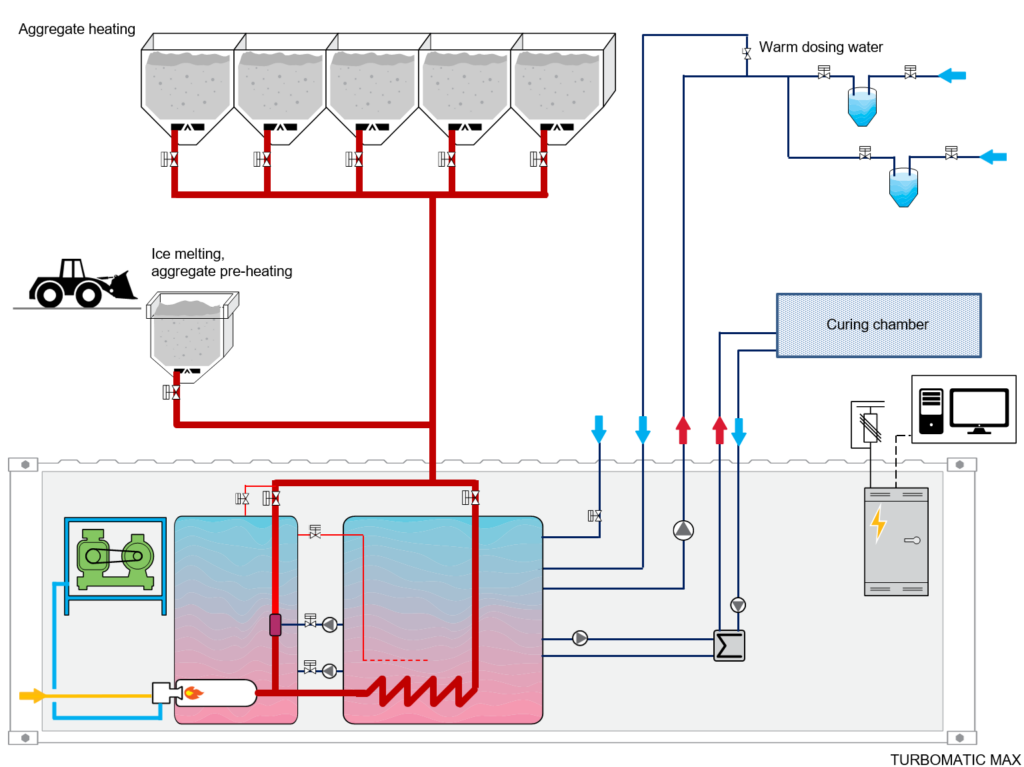
Service Makes the Difference
At the end of 2021, Polarmatic carried out a wide customer satisfaction survey among their annual maintenance customers, and the excellent survey results exceeded all expectations. Mr. Pignatelli gladly confirms this:
« Both the products and service from Polarmatic are great. We also appreciate that Polarmatic offers an annual maintenance service for the systems they supply, to ensure that the unit is well maintained and in good working order for the new heating season. I can highly recommend the Polarmatic system to other concrete producers in the industry. TURBOMATIC™ has truly helped us to achieve consistent concrete production year-round. »
John Pignatelli, Best Way Stone Ltd.
Solution
TURBOMATIC/CUREMATIC Thermal Energy Unit fuelled by natural gas
Batch Plant
Production: | Block and Paver Plant |
Number of mixers: | 2 pcs, 2 yd3 (1,5 m3) and 1 yd3 (approx. 0,8 m3) |
Number of aggregate bins: | 5 pcs |
Production rate: | 40 yd3 (30 m3) / h at 70°F (21°C) concrete temperature |
Ambient conditions: | Min. temperature: 20.6°F (-6,3°C) Min. aggregate temperature: 23°F (-5,0°C) |
Heating – Curing Solution
Total capacity: | 2.6 MBTU – 0,75 MW |
Fuel: | Nat. gas (Biogas capable) |
Structure: | 1 x 20 ft sea container MODEL PME-MAX 750 G 1 x Water heating system with warm air blowers for heating batch plant 1 x Aggregate heating system with temperature measuring system 1 x Water heating system for warm air curing w/ RH adjustment in curing chamber |